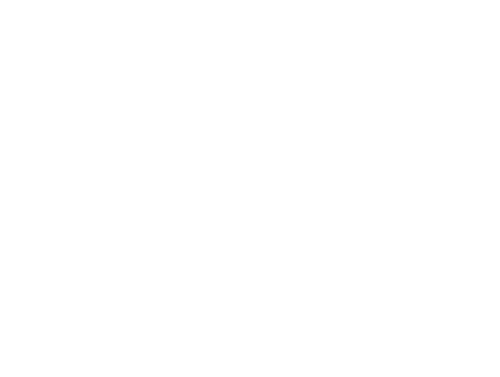
Tangle and Twist-Free Packaging Technology.
REELEX tangle-free technology is a patented method of winding a filamentary product (such as cord, wire, cable or tubing) into a figure-eight coil on a specialized coiling machine.
This unique coil dispenses from the inside-out without twists, tangles, snags or overruns. Because the coil does not rotate during payout, there is no inertia, and thus no need for payoff stands or brakes. And since the coil does not require any moving parts as a means of dispensing the product, it may be packaged in a wide variety of package shapes and materials, or simply placed in a cardboard box.
Why REELEX? Watch this.
Why a figure-eight coil?

No Tangles.
Tangle-free by nature.
REELEX coils unwind from the inside-out through a payout tube. Each layer of the coil is separated by a crossover, which prevents knots and tangles from forming between loops. Innovative tube designs ensure smooth payout, even in cold temperatures or when packaging less-flexible products.
Just place the REELEX package on a surface and pull as hard as you need to. When you stop, payout stops.

No Twists.
Opposing twists equals no twist.
While winding, the REELEX wind imparts a half-twist in one direction, then an equal half twist in the opposing direction. These twists cancel out when dispensing from the coil, effectively eliminating twist from the product.
Unlike linear-wound coils, which exhibit continuous twist on payout, REELEX packages eliminate twist – providing smooth, uninhibited payout performance.

No Overruns.
No rotation equals full control.
REELEX coils are self-supporting and do not rotate during payout. As a result, the end-user experiences low tension, zero inertia, and can pull product 30% faster than if using reels. Installers experience payout that simply flows out of the package and stops when they stop.
What’s more, no rotation means stands, brakes, and payoffs are eliminated; as is any chance of overruns, resistance or tangling.

No Pigtails.
Bye piggy.
Opposing twists means the curling or “pigtail” effect exhibited by products with memory is eliminated. Linearly wound methods (spools, reels and linear coiling) impart continuous bending into the product when winding.
REELEX eliminates this bending by delivering product across the winding head, and doing so more than once per rotation. This eliminates the continuous bend in the product, which means the memory effect is broken up and is no longer evident after payout.
Less Waste, More Environmentally-Friendly

Less environmental Impact, but also less hassle.
No internal structure means there is no bulky packaging components to dispose of. Empty boxes are broken down quickly and easily, saving time on the job.
Fewer bulky components means REELEX allows jobsite waste volume to be reduced by up to 60% compared to reels and spools.
Unlike spools, the materials REELEX packages use are easily separated for recycling, are often 100% recycled, and are 100% recyclable.
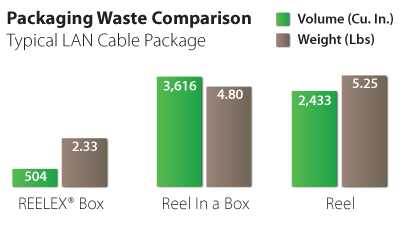
Just Plain Fast.
In REELEX’s Fast Pulls series, we tie one end of the cable to a fast car to see how quickly we can pull wire from a REELEX package.
How does this translate to real life? We’re not sure, but we do know that REELEX’s ability to dispense cable without tangles, twists, rotation or inertia allows cable installers to complete jobs up to 30% faster than using spools or reels.
The REELEX® Coil.
Control Over Size, Fit and Performance.
REELEX machines can adjust every aspect of how the coil is wound, including altering the coil’s layer density, payout hole configuration and spacing between layers. Each of these parameters effect overall coil size as well as payout performance.

Where it all happens.
The product enters the guide tube and exits the wire guide which are connected to the traverse. The traverse is controlled via unique electronics and REELEX-approved drives for precise layering. The traverse moves back and forth and moves in sync with the rotation of the mandrel as the coil is wound.
The coil builds along the walls of the endforms, which require mathematically-derived curves designed to maintain coil shape and density. When the coil is finished winding, the outer endform attached to the endform arm is pneumatically removed, and the mandrel segments collapse. The coil is now removed from the machine and placed into its final package.
Parts of the REELEX Coil

Coil Parameters

Payout Hole
The key to payout performance.
The hole size setting on all REELEX machines can be adjusted in degrees of circumference. The larger the setting, the larger the payout hole, however the coil size will also increase.
Any payout hole larger than 120° may produce a coil that may collapse or cause the product to slip. The hole size should be chosen so that a the machine or operator does not have a problem inserting the tube. REELEX I coils feature payout holes up to 60°, and REELEX II exhibit holes of 60° and greater.
REELEX machines can also alter the shape of the hole via Taper and Shift settings. These settings can be used to “tweak” the coil, but also serve an important role when coiling especially slippery products or extremely long coil lengths, as they maintain payout hole integrity.

Gains and Crossovers
Art and science.
If you picture a series of figure-eights stacked atop one another, the “gain” controls the distance between these layers. Where the product crosses over itself is the “crossover”. These must be staggered, or else the coil would not be cylindrical.
The gain adjustments control the distances between wraps in a layer. Generally, the lower the gain, the less negative space in the coil and therefore the coil will be denser and result in a smaller diameter. However, if the gain goes too low the coil will start to increase in diameter, as layers have no where to go but build atop one another.
In addition to fine-tuning the diameter of the coil, the gains also adjust tension placed on the product within the coil. Higher gains will help ease the tension within the coil if the product being wound is sensitive to pressures or deformation.

Density Setting
Small adjustment, big effects.
The Density Program staggers the location of the crossovers so they occur at irregular intervals. In addition to allowing for increased coil density, the shifting of the crossovers have a significantly positive effect on the electrical performance of data cables such as Category 5e, Category 6 and more.
This means products that previously may have performed marginally in electrical testing can now be packaged in REELEX with little or no degradation in performance. Density is especially useful in packaging foiled or shielded products, as well as high-end LAN cables such as Category 6a and Category “7” / “8”.
Coil Types
REELEX I | REELEX II | |
![]() | ![]() |
|
Payout Hole Size | 40 to 60 Degrees | 70 Degrees and Higher |
Payout Tube | Two-piece plastic tube comprised of a payout tube and a snap-on locking ring with wire clip. Length: 2in to 6in length (5cm to 15cm) Diameter: ø 0.75in (2cm) | Single-piece funnel-shaped payout tube that “drops in” to the coil. Uses box design to capture payout tube (no locking ring). Length: 6in length (15cm) Diameter: ø 2.50in (6.35cm) at product entry |
Recommended Product Diameter Range | Minimum: ø 0.01in (0.25mm) Maximum:ø 0.15in (3.81mm) | Minimum: ø 0.10in (2.5mm) Maximum: ø 0.50in (12.7mm) |
Typical Supported Coil Diameters | ø 9in to ø 16in (23cm to 41cm) | ø 12in to ø 22in (30.5cm to 56cm) |
Typical Product Examples | Security/alarm wire, audio cables, THHN, small single-conductor building wires, small fiber optic cables, hookup wires, plastic tubing. | High-performance structured cabling (Cat 5e, Cat 6 and up), shielded cables including coaxial cables, less flexible products such as some drop wires. |
What Mandrel to Use?
The diameter of the mandrel defines the inside diameter of the REELEX coil. In general, the mandrel size should be selected based on the bend radius of the product.
Three standard size mandrels are available, with others available upon request.
Because a larger mandrel does not always equal a larger coil, the mandrel size should be selected based on the product OD. In general, a bigger mandrel is better for payout performance, while a smaller mandrel is better for maintaining coil integrity of highly flexible products.
For determine the estimated coil size of your product, consult the packaging calculator.
Coil Diameter by Product Size and Mandrel Diameter
Containers

Because the REELEX coil does not rotate, products wound in REELEX do not depend on the package itself to dispense properly. Because the package is literally just a container, the coil can be packaged in a unlimited number of designs and materials. This flexibility allows manufacturers to present their products in unique and innovative ways; providing opportunities for product differentiation and competitive advantage.
This flexibility also allows REELEX to be one of the most environmentally-friendly packaging options currently available to linear products – providing a plethora of material and package design methods to achieve presentation, usability or environmental goals.
Package Type | REELEX I Box | EcoCore Box | REELEX II Box |
![]() | ![]() | ![]() |
|
Typical REELEX Coil Diameters | ø 9in to ø 16in (23cm to 41cm) | ø 9in to ø 22in (23cm to 56cm) | ø 12in to ø 22in (30.5cm to 56cm) |
Supported Payout Tube | REELEX I | EcoCore | REELEX II |
Material | Cardboard | Cardboard | Cardboard |
Estimated Cost | $1.50-$2.50 per box* | $1.25-$2.50 per box* | $1.75-$3.00 per box* |
Typical Package Examples | 500 ft (150m): Security/alarm wire, audio cables, building wires. 1,000 ft (305m): Security/alarm wire, audio cables, building wires. | 500 ft (150m): Most flexible low-voltage products and fiber optic cables. 1,000 ft and up (+305m): Most flexible low-voltage products and fiber optic cables. | 500 ft (150m): Structured cabling, most low-voltage cables, and fiber optic cables. 1,000 ft and up (+305m): Structured cabling and fiber optic cables. |
Package Type | ProFlex | SlingPack | Reuser Case |
![]() | ![]() | ![]() |
|
Typical REELEX Coil Diameters | ø 9in to ø 16in (23cm to 41cm) | ø 9in to ø 16in (23cm to 41cm) | ø 15in to ø 16.5in (38cm to 42cm) |
Supported Payout Tube | REELEX I or EcoCore | REELEX I or EcoCore | Any |
Material | Plastic Shrink Film | Stretch Wrap (Coil), Cardboard (Sling) | Injection-Molded Plastic |
Estimated Cost | $1.00-$2.00 per bag* | $1.00-$2.00 per package* | $20 per case, but reused frequently. |
Typical Package Examples | 250 ft (75m): Single-conductor building wires, flexible low-voltage products and fiber optic cables. 500 to 1000 ft (150-305m): Smaller flexible low-voltage products and fiber optic cables. | 250 ft (75m): Structured cabling, low-voltage products and fiber optic cables. 500 to 1000 ft (150-300m): Single-conductor building wires, flexible low-voltage products and fiber optic cables. | 750 ft (230m): RG6 and other Coaxial or Drop Cables. 1,500 ft (500m): Category 5e and other low-voltage cables. |
Used by the World’s Most Prominent Cable Manufacturers
Sold under various brand names by the world’s leading wire and cable manufacturers, REELEX has become the standard packaging system for “last-mile” lengths of structured and low-voltage cabling such as Category 5e, Category 6, security/alarm cables, instrumentation cables, coaxial cables, and is quickly becoming the preferred package for many other types of products like fiber optics, building wire, plastic tubing, and more.
